L'Itération Produit Rendue Facile avec l'Impression 3D : du Prototype au Produit Final
L'itération est un processus incontournable dans le développement de produits, surtout dans un environnement où la concurrence et l'innovation technologique imposent un rythme de création toujours plus rapide. L'itération permet d'améliorer constamment un produit en passant par plusieurs versions, chacune affinée par rapport à la précédente, afin d'arriver à un résultat final qui répond parfaitement aux besoins du marché et des utilisateurs.
Dans ce contexte, l'impression 3D est devenue un outil révolutionnaire pour les équipes de conception et de développement. Il est désormais possible de créer des prototypes fonctionnels en un temps record, d'explorer diverses options de conception et d'ajuster rapidement les produits avant leur mise en production. L'impression 3D offre ainsi une solution idéale pour un développement itératif, où chaque prototype peut être testé, modifié et amélioré à moindre coût et dans des délais réduits.
Que ce soit pour une validation du type "proof of concept" ou pour les dernières itérations d’un produit avant sa commercialisation, l'impression 3D est un atout majeur. Dans cet article, nous explorerons comment l'impression 3D simplifie chaque étape du processus d'itération, du prototype initial jusqu'au produit final, tout en détaillant les bénéfices concrets de cette technologie pour l'optimisation produit.
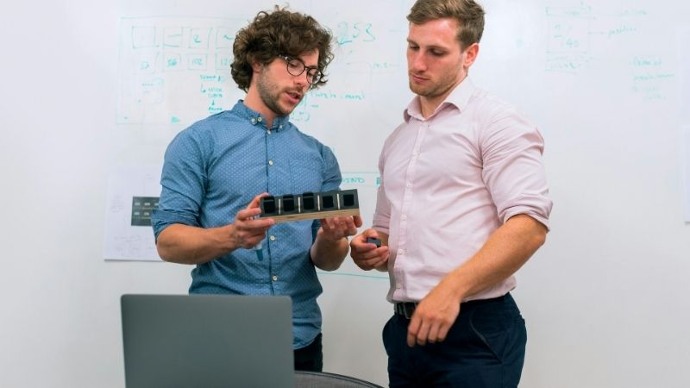
A quoi sert un prototype ?
Un prototype est la première version physique ou numérique d'un produit en cours de développement. Il s’agit d’une maquette fonctionnelle ou d’un modèle expérimental qui permet de matérialiser une idée initiale, et de la tester avant une production à grande échelle. Ce processus est crucial pour toute entreprise souhaitant lancer un produit sur le marché, car il offre la possibilité de vérifier la faisabilité technique et de tester les premières fonctionnalités du concept.
Le prototypage est une étape essentielle dans le cycle de développement produit. Il permet de transformer un concept abstrait en une forme tangible, facilitant ainsi la validation du concept initial et l’ajustement du produit avant de s'engager dans des phases coûteuses de production. Les prototypes servent également de support pour la collecte de feedback auprès des utilisateurs et des parties prenantes, offrant ainsi une première vision de l'expérience utilisateur potentielle.
Présentation d'un prototype de produit
Dans le cadre du développement itératif, les prototypes jouent un rôle central. Ils permettent d’identifier les améliorations à apporter, que ce soit au niveau du design, de l'ergonomie ou de la fonctionnalité. Le prototypage rapide, notamment grâce à l'impression 3D, a transformé cette phase du processus. Les équipes peuvent désormais tester et modifier rapidement des modèles sans perdre de temps ou de ressources, tout en explorant plusieurs directions de conception avant de valider la version finale.
En résumé, le prototype est un outil clé pour la validation conceptuelle et la réduction des risques avant la mise en production d’un produit. Il permet de valider des hypothèses et d’ajuster le produit en fonction des essais fonctionnels, garantissant ainsi un produit optimisé à la sortie.

Prototype en impression 3D de cercle pour poubelle de tri (collaboration entre DAGOMA et DIZY)
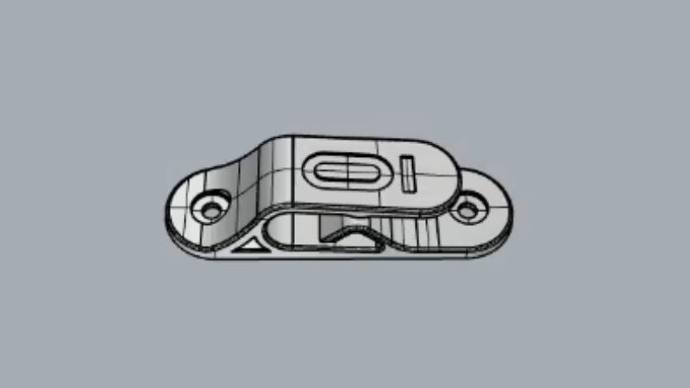
L'itération de prototypes
L'itération est un processus central dans le développement de tout produit innovant. Il s'agit de la répétition continue d’un cycle de conception, avec des ajustements progressifs à chaque version, dans le but d'améliorer le produit à chaque étape. Lorsqu'il s'agit de prototypes, l'itération permet de passer d'une version simple à une version affinée, en intégrant des améliorations basées sur les résultats des tests et les retours des utilisateurs.
Le cycle itératif repose sur la capacité à identifier rapidement les points faibles d’un prototype et à les corriger avant de passer à la version suivante. Ce processus de raffinement progressif permet d’optimiser à la fois la performance, l’ergonomie et la fonctionnalité d'un produit. À chaque itération, une nouvelle version du prototype est créée, testée et évaluée, avec l'objectif de se rapprocher toujours plus du produit final idéal.
Modélisation 3D d'une pièce pour un clip de fermeture de sac avant fabrication de plusieurs séries de prototypes
L'un des aspects clés de l'itération est la boucle de rétroaction. Après chaque test, des données précieuses sont collectées et analysées, ce qui permet d'apporter des modifications pertinentes au prototype. Cette approche permet d'éviter les erreurs coûteuses qui pourraient survenir si le produit était directement mis en production sans ces cycles d’amélioration. De plus, elle s’inscrit dans une logique d'optimisation continue, où chaque version du prototype est meilleure que la précédente.
L'impression 3D joue un rôle crucial dans ce processus d’itération rapide. Grâce à la fabrication additive, les prototypes peuvent être modifiés et produits en un temps record, offrant ainsi une flexibilité exceptionnelle dans le cycle de développement. Les entreprises peuvent ainsi tester différentes options de conception en un laps de temps réduit, tout en minimisant les coûts associés à la création de nouvelles versions physiques.
En conclusion, l'itération des prototypes est indispensable pour garantir que le produit final sera performant, fonctionnel et adapté aux attentes des utilisateurs. Ce processus itératif, rendu plus efficace grâce à l’impression 3D, permet de concevoir des produits plus rapidement et avec une qualité optimisée à chaque étape.
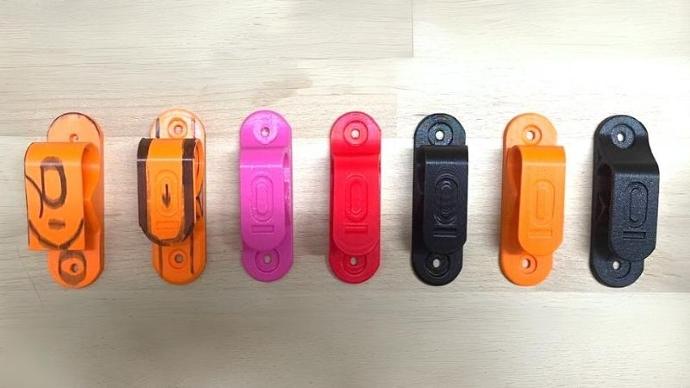
Séries de prototypes d'un clip de fermeture pour un sac
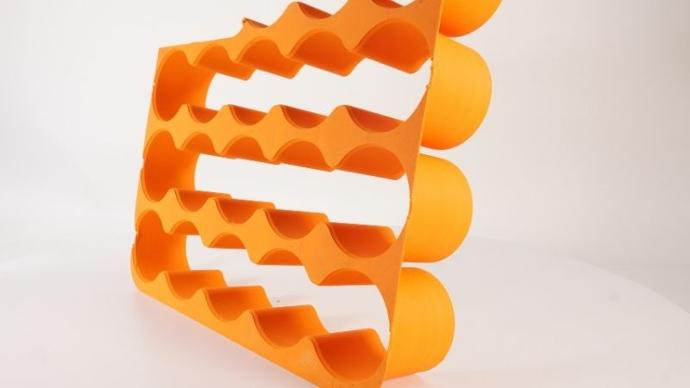
Le prototype comme "proof of concept"
Le proof of concept (ou POC) est une étape essentielle dans le processus de développement de tout nouveau produit ou service. Il s’agit d’une démonstration préliminaire visant à valider la faisabilité d'une idée ou d'un concept avant d'investir des ressources plus importantes dans son développement complet. Le proof of concept permet de s'assurer que les hypothèses initiales sont correctes et que le produit envisagé peut effectivement fonctionner dans des conditions réelles.
Dans le domaine du prototypage, le proof of concept joue un rôle crucial en fournissant une première validation technique et fonctionnelle du concept. À ce stade, il ne s'agit pas encore de créer un produit final, mais plutôt de vérifier que l'idée est viable d’un point de vue technologique et qu’elle peut évoluer vers un produit plus élaboré. En réalisant un POC, les entreprises minimisent les risques en testant le cœur du projet avant de passer à des étapes de conception plus coûteuses, comme le prototypage détaillé ou la production en série.
Prototype pour une solution de rangement de flacons dans un casier de transport
L'un des principaux avantages du proof of concept est qu'il offre une opportunité de détecter et d’anticiper les problèmes potentiels dès le début. Que ce soit au niveau des matériaux utilisés, des technologies employées ou des fonctionnalités à intégrer, le proof of concept permet de valider ces éléments clés avant d’engager des ressources supplémentaires. De plus, le POC est souvent utilisé pour convaincre les investisseurs ou les parties prenantes de la viabilité d'un projet, en leur présentant une version simplifiée mais fonctionnelle de l’idée.
L'impression 3D joue ici un rôle majeur. Grâce à elle, il est possible de créer rapidement un prototype fonctionnel basé sur un proof of concept. Par exemple, dans le développement de produits industriels ou de dispositifs médicaux, un POC imprimé en 3D permet de valider les aspects critiques du design ou de la structure en quelques jours, là où les méthodes traditionnelles prendraient plusieurs semaines. L'impression 3D facilite ainsi la création de maquettes pour tester des concepts avant de lancer le cycle complet de développement.
En conclusion, le proof of concept est une phase indispensable pour tout projet d’innovation. Il permet de confirmer que l’idée peut être mise en œuvre techniquement avant de poursuivre les phases plus complexes du développement, telles que la fabrication de prototypes avancés ou la production à grande échelle. L'impression 3D renforce cette étape en offrant une méthode rapide et flexible pour concrétiser les premières idées de façon tangible.
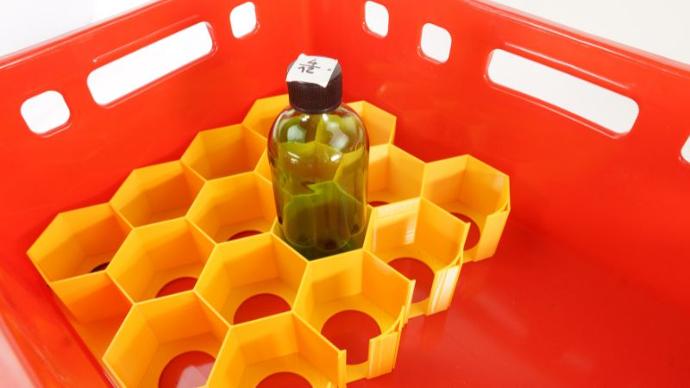
Prototype pour une solution de rangement de flacons dans un casier de transport en situation
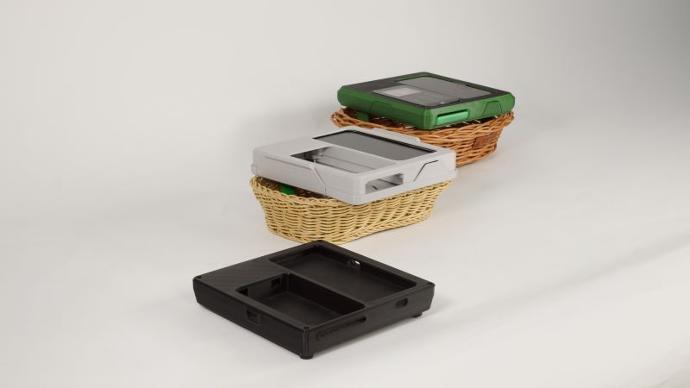
Le prototype pour l’amélioration et l’optimisation produit
L'amélioration et l'optimisation sont des étapes importantes qui interviennent tout au long de la vie d'un produit. Elles visent à perfectionner les aspects fonctionnels, esthétiques et ergonomiques du produit, afin de garantir qu'il répond aux attentes des utilisateurs et qu'il est / qu'il reste compétitif sur le marché. L'amélioration d'un produit repose elle aussi sur un cycle itératif où chaque nouvelle version est testée et affinée. Les prototypes jouent encore une fois un rôle fondamental dans ce processus. Avec l’impression 3D, il est possible de produire rapidement différentes versions d'un même produit, intégrant à chaque fois des ajustements basés sur les retours des tests et des utilisateurs. Cette capacité à tester et modifier rapidement le design permet de corriger les défauts identifiés et d'introduire de nouvelles fonctionnalités selon les besoins des utilisateurs.
L'optimisation d’un produit concerne plusieurs aspects clés : les performances, la durabilité, l’efficacité, l’ergonomie. L’objectif est d’atteindre la meilleure version possible du produit. Une optimisation peut se concentrer sur la conception d'une pièce pour optimiser sa résistance, son poids, ou sur des ajustements ergonomiques pour offrir une meilleure prise en main.
Plusieurs versions d'un dispositif flexible de collecte de dons pour les églises. Voir le cas STIPS
L'une des grandes forces de l'impression 3D dans cette phase d'optimisation est la flexibilité qu’elle offre. En permettant de tester rapidement différentes configurations de design ou d’intégrer des modifications sans avoir à refaire des moules ou des outillages, elle accélère considérablement le processus d’optimisation produit. Cette technologie permet également de simuler diverses conditions d'utilisation pour vérifier la robustesse du produit dans des situations réelles.
De plus, les améliorations apportées grâce aux retours des utilisateurs sont un aspect essentiel de l'optimisation. Le retour direct des premiers utilisateurs permet d'identifier des points de friction qui n'avaient pas été envisagés lors des premières phases de développement. Ces feedbacks sont ensuite intégrés dans les itérations suivantes du produit, garantissant une amélioration continue.
En résumé, l'amélioration produit repose sur un processus itératif visant à perfectionner le produit à chaque étape. L’optimisation permet de garantir que le produit final est non seulement fonctionnel, mais également efficace, durable et adapté aux besoins des utilisateurs. L'impression 3D facilite grandement cette démarche en offrant une méthode rapide et économique pour tester, modifier et améliorer les prototypes jusqu'à la version optimale du produit, et même après sa commercialisation.
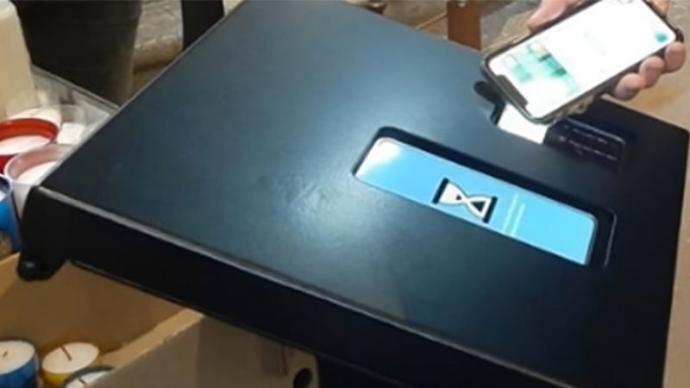
Dispositif flexible de collecte de dons en situation, après validation du dernier prototype
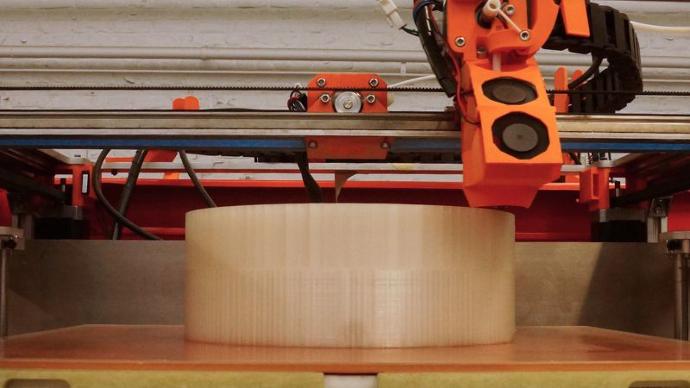
Impression 3D et prototypage rapide
L'impression 3D a révolutionné le prototypage rapide, en permettant aux entreprises de réduire considérablement les délais de création des premières versions de leurs produits. Contrairement aux méthodes traditionnelles, qui nécessitent des outillages coûteux et du temps pour fabriquer des pièces, l’impression 3D offre une solution rapide et flexible. Grâce à la fabrication additive, il est possible de créer des objets directement à partir d’un fichier numérique en superposant des couches de matériau, qu'il s'agisse de résine, de plastique ou de métal.
Dans le contexte du développement itératif, l'impression 3D permet de tester rapidement différentes conceptions, de modifier le prototype au fur et à mesure des ajustements et de produire des versions successives en quelques heures, ou en quelques jours. Cette flexibilité offre un avantage concurrentiel important, car elle permet de répondre plus rapidement aux besoins du marché tout en réduisant les coûts associés aux modifications de conception. Chaque cycle de tests et d'améliorations peut ainsi être effectué à un rythme plus soutenu, optimisant le temps de développement.
Impression 3D en cours pour un composant de prototype de lombricomposteur
L’un des principaux atouts de l’impression 3D dans le prototypage rapide est sa capacité à produire des prototypes fonctionnels. Ces pièces ne sont plus seulement des modèles visuels ; elles peuvent être testées dans des conditions déterminées pour évaluer leur performance, leur durabilité ou leur ergonomie.
De plus, l’impression 3D favorise la personnalisation des prototypes. Les concepteurs peuvent ajuster chaque version en fonction des retours d’expérience ou des exigences spécifiques du projet. Cette capacité à personnaliser rapidement et à faible coût chaque prototype contribue à la création de produits plus innovants et mieux adaptés aux besoins des utilisateurs finaux.
En résumé, l’impression 3D a transformé le prototypage rapide en une méthode incontournable pour tout projet de développement itératif. Elle permet non seulement de réduire les coûts et les délais, mais elle offre également une flexibilité sans précédent pour tester, modifier et optimiser les conceptions avant la mise en production finale. Cette technologie ouvre de nouvelles possibilités pour les industries cherchant à accélérer leur innovation tout en maintenant une qualité optimale du produit.
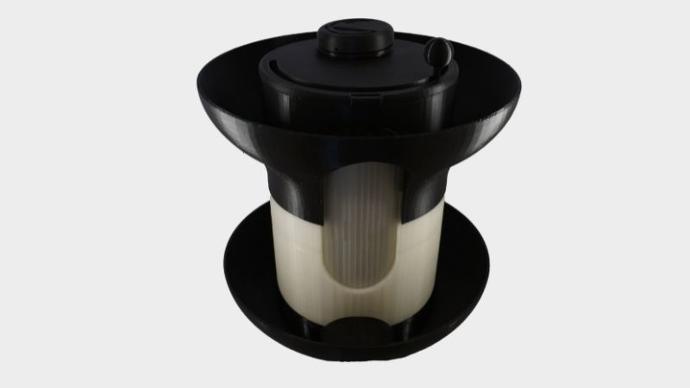
Prototype de lombricomposteur complet après sa fabrication en impression 3D
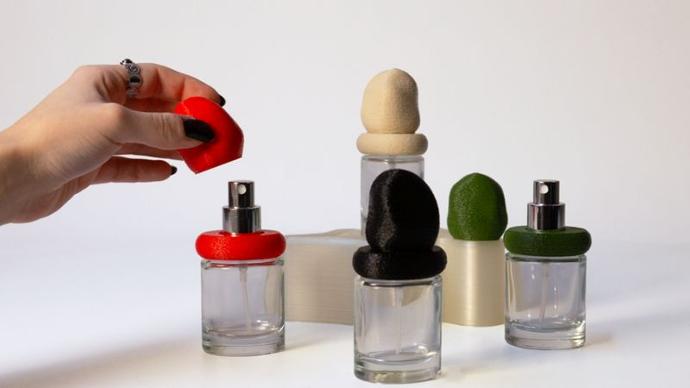
Le cas de FASCENT : prototypage de bouchons de parfum
FASCENT est une marque de parfum qui a su combiner innovation technologique et créativité artistique pour réinventer un élément important dans le secteur de la parfumerie : les bouchons de flacons de parfum. L'objectif de FASCENT était clair : créer un bouchon de parfum à la fois fonctionnel et esthétiquement unique, capable de refléter la personnalité de la marque tout en se démarquant sur le marché.
Pour répondre à ce défi, FASCENT s'est tourné vers DAGOMA. L’utilisation de l’impression 3D a été un facteur clé dans la réalisation de ce projet, permettant à la marque de repousser les limites de la fabrication traditionnelle. Grâce à cette technologie, FASCENT a pu explorer des formes complexes et des textures inédites, impossibles à obtenir avec des méthodes conventionnelles. Vous pouvez en découvrir plus à partir de notre article dédié.
Collection de bouchons de parfum réalisés en impression 3D par DAGOMA pour FASCENT
Lors des premières phases du projet, DAGOMA a mis à disposition son expertise en modélisation 3D et a fourni des recommandations techniques pour concevoir un bouchon sur-mesure. L'utilisation de l’impression 3D a permis d’accélérer le processus de prototypage, de tester différentes versions du bouchon et d'intégrer des ajustements basés sur les tests fonctionnels et esthétiques. À chaque nouvelle version, FASCENT a pu affiner le design et les fonctionnalités de son bouchon en fonction des retours d'un échantillon test d'utilisateurs.
L'un des avantages les plus significatifs de l'impression 3D dans ce projet a été la possibilité de personnaliser les différentes versions du bouchon. En ajustant rapidement les modèles et en testant différentes configurations, FASCENT a pu trouver la combinaison parfaite entre esthétique et fonctionnalité. Cette flexibilité, offerte par la fabrication additive, a permis à la marque d'explorer des options de design beaucoup plus audacieuses que celles disponibles avec des méthodes de production traditionnelles.
La collaboration entre FASCENT et DAGOMA a abouti à la production d'une première série de 1 000 bouchons de parfum, tous réalisés grâce à l’impression 3D.
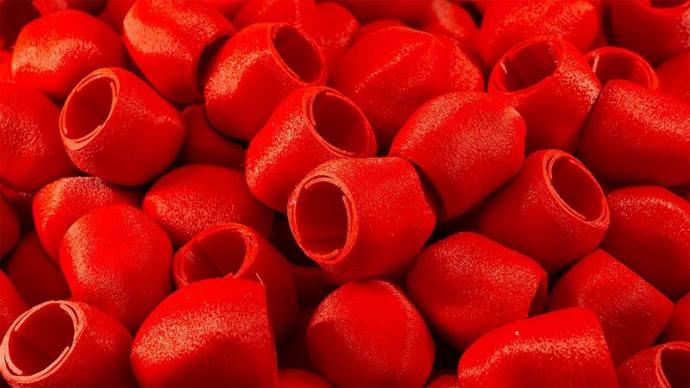
Fabrication en série de bouchons de parfum pour FASCENT
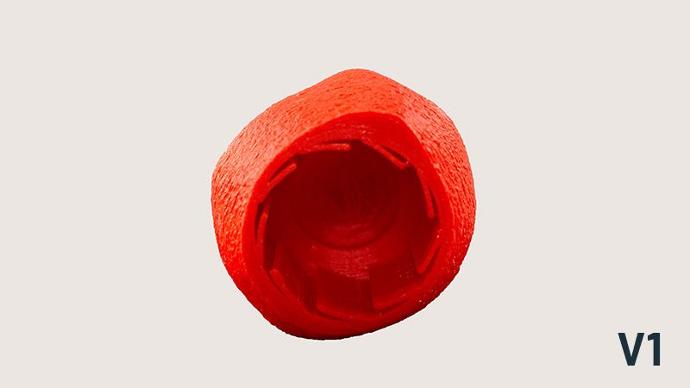
L’itération des bouchons de parfum de FASCENT
La première version du bouchon de parfum de FASCENT a été conçue pour être esthétiquement distincte et parfaitement adaptée à la personnalité de la marque.
Cependant, après avoir produit une première série de bouchons, les utilisateurs ont rencontré un problème : une fois les flacons remplis, le serrage du bouchon n'était pas assez important. Le mécanisme de fixation, constitué de picots au milieu du bouchon, s'avérait trop souple pour maintenir correctement le bouchon sur le flacon, surtout avec le poids supplémentaire des liquides.
Ce retour d’expérience a mis en lumière le besoin de renforcer la fixation du bouchon.
Version 1 du bouchon de parfum FASCENT
Prototype 2
Pour la deuxième version (V2), DAGOMA a collaboré avec FASCENT et a retravaillé les pattes du bouchon, afin de les rendre plus rigides et d'améliorer le serrage. Ces pattes, qui étaient initialement longues et fines, ont été épaissies pour apporter plus de stabilité. La modification consistait à passer d'une épaisseur de couche de 0,4 mm à 0,8 mm lors de l'impression 3D, ce qui a permis d'augmenter la rigidité et la solidité du système de fermeture.
Cependant, cet ajustement a entraîné un autre défi : l'élargissement nécessaire des pattes modifiait le design extérieur du bouchon, ce qui ne répondait alors plus au cahier des charges esthétiques de FASCENT. Bien que cette version améliorée ait résolu le problème de fixation, elle ne correspondait pas aux exigences de design de la marque.
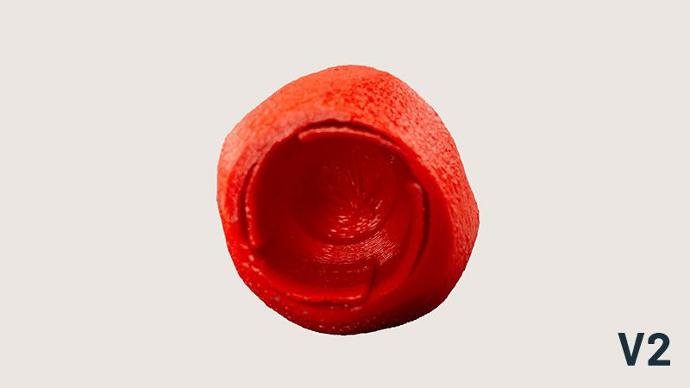
Version 2 du bouchon de parfum FASCENT

Prototype 3
Une troisième version (V3) a alors été conçue, avec des pattes plus grosses dans un bouchon plus petit, afin de revenir à un design plus proche de l’original.
Cependant, cette nouvelle itération a de nouveau révélé un problème similaire à celui de la première version : la souplesse du bouchon n’était pas suffisante, ce qui l’empêchait de s’adapter aux tolérances de taille variables des pompes installées sur les flacons.
Le défi consistait donc à trouver une solution qui offrirait à la fois un maintien ferme et une apparence élégante, conforme aux attentes esthétiques de FASCENT.
Version 3 du bouchon de parfum FASCENT
Prototype 4 et version finale
La solution a finalement été trouvée dans la quatrième version (V4). Pour cette dernière itération, l'équipe de DAGOMA a retravaillé l'orientation des pattes en leur donnant une forme évasée : elles étaient étroites à la base et larges à l'ouverture du bouchon.
Ce changement a permis d'améliorer considérablement le serrage tout en respectant le design original du bouchon. Avec cette solution, FASCENT a obtenu un bouchon qui répondait à la fois aux critères fonctionnels et esthétiques.
Cette collaboration entre FASCENT et DAGOMA illustre parfaitement l'importance de l'itération produit dans le développement d'un élément aussi spécifique qu’un bouchon de parfum. Grâce à l’impression 3D, chaque version a pu être testée, modifiée et améliorée jusqu’à atteindre la version finale idéale, tant sur le plan fonctionnel qu'esthétique. Tout ceci a été réalisé en un temps record, avec un coût maîtrisé.

Version 4 du bouchon de parfum FASCENT
Evolution de la modélisation en 3D pour le bouchon de parfum de FASCENT, travail spécifique sur le système de serrage
Evolution de la modélisation en 3D pour le bouchon de parfum de FASCENT, vues intérieures et extérieurs
L'itération produit est un processus indispensable pour le développement de solutions innovantes et optimisées. Grâce à l'impression 3D, il est désormais possible de tester, ajuster et améliorer un produit en un temps record, avec une flexibilité inégalée. Chaque prototype, qu'il s'agisse d'une première version expérimentale ou d'une version plus aboutie, joue un rôle clé dans l'évolution du produit final.
L’exemple de la collaboration entre FASCENT et DAGOMA montre parfaitement comment ce processus itératif permet de répondre aux défis techniques tout en respectant des exigences esthétiques. L'impression 3D a non seulement accéléré le cycle de prototypage, mais elle a également offert à FASCENT la capacité d'explorer des designs originaux, d'intégrer des modifications rapidement et de produire un bouchon de parfum à la fois fonctionnel et unique.
En conclusion, l'itération, soutenue par l'impression 3D, permet aux entreprises de rester compétitives dans un marché en constante évolution. Elle offre une approche agile pour transformer des concepts en produits finalisés, tout en garantissant une optimisation continue à chaque étape du développement. Que ce soit pour des prototypes ou des produits finaux, l'impression 3D facilite ce processus d'amélioration, réduisant les risques et maximisant l'efficacité de la production.
Si vous aussi vous souhaitez bénéficier de l'accompagnement de DAGOMA pour la réalisation de vos prototypes, notre équipe se tient à votre disposition pour pouvoir concrétiser votre projet !
Vous aussi vous évoluez dans le secteur du "Prototypage & Design" et vous cherchez à fabriquer des pièces techniques ?
Nos équipes se tiennent à votre disposition pour pouvoir vous renseigner ! N'hésitez pas à nous contacter à l'aide du formulaire ci-dessous.